Windows and A LOT of insulation
A short but busy week of dawn to dusk work hours for both of us and...suprise...the return of mud!
Tuesday our windows were delivered, and Vern and I were on site bright and early to unload them with the assistance of a very nice Canadian truck driver.Over last weekend we started trying to set the 12x12 glass blocks by first building and painting 2x6 boxes, adhering the blocks to the boxes with silicone, and then setting and attaching them to the openings. We completed a few and decided we weren't happy with the results so we're on to plan B using laminated plywood.
We also got a start on installing our windows. All of the openings in the ICF need to be roughed out with lumber to provide a nailing surface for the window flanges, and we've spent most of the last four days cutting, gluing, screwing and power nailing toward this cause. As expected, the the upper level living room windows are proving to be quite a challenge. Fortunately, Vern has some pretty extensive rock climbing experience and very long arms, so he did the work up on the extension ladder while I acted as tool jockey and gopher on the shorter ladder. Getting some seriously heavy, 48 x 48 triple pane windows up 15 or 20 feet is going to be interesting, but at least we've gotten the more labor intensive part of the job done. Here's a shot of the front with a few of the smaller windows and glass block in place:
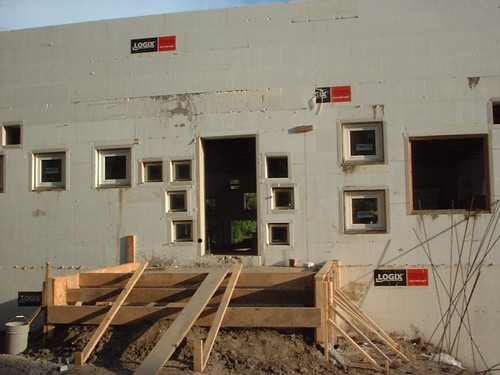
and one of the the big, south facing windows that looks out onto the lower roof deck:
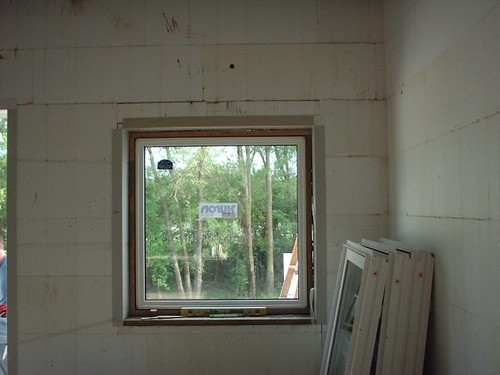
On Friday we received our interior framing lumber and the acres of roof insulation panels. These were delivered in an almost full 18 wheeler trailer that I thought we would never find the front of, and again, it was just Vern and I and a nice driver there to unload. Although the bundles aren't heavy, they're 48" square and very cumbersome so we got our morning workout in while the neighbor kids watched and looked confused.
Since we supplied this insulation rather than our roofer as would be typical, we are responsible for placing it, leading to the dilemma of how to get it all up onto the roof. I think there are around 100 bundles, most with five sheets of 5" thick foam. Fortunately we had a great friend volunteer to help us out today, and a rainy-day adventure that was intended as a plan and organize mission turned out to be an all out effort, and the three of us got all of these bundles onto the roof in about three hours using the straps and a rope. And after a dry week (finally!) the rain turned everything into a mud pit again to make the job even more fun. An after-work dinner at the local drive-in drew quite a few strange looks for our little trio of mud people. This picture was taken after about half the bundles had already made their way up:

Tomorrow we'll get a start on placing the two 5" layers plus the layer of tapered panels that provide the pitch for drainage after we use the shopvac to pump off the few inches of water that's up there with nowhere to go. We hope to make a bunch more progress on the window installation tomorrow with some extra help and equipment, and we're scheduled for roofing and the stoop on Wednesday if the weather cooperates. Hopefully we'll be dried in by the end of the upcoming week and be able to start on interior framing and schedule plumbing and electrical rough-in.
4 Comments:
Just found your site, Splatgirl - love it! I've read most of it, you are an ambitious girl!! Question, did you run into any problems with your door thresholds being too high b/c you left the concrete? I've found they all tend to expect flooring to be installed and would leave a rather large tripping hazard of threshold if installed the regular way. How did you handle this? Or any creative ideas to throw my way for handling it? It is a new build, so I can do pretty much anything. THANKS! -- sheila
Hi Shelia
Really?
I sort of don't get how this would be an issue unless the thresholds are like 3" tall or something. Doors don't open themselves, after all.
Keep in mind that there does need to be some clearance above the finish floor for the door to swing freely, and nothing bugs me more than a door that won't swing open across a rug at an entry point. I would NEVER try to set the door threshold equal to the finish height of the floor...what if it's not 100% level across the sweep of the door? What if you want a nice plush rug there?
One could always put a little bevel strip there which would be a much easier fix than trying to deal with a door that won't operate because it's too low.
cheers and good luck with your project!
Thanks for answering! I should have been clearer, I was thinking of the sliding glass patio doors in particular...they seem to have a large at least 1" threshold that's just a black piece of metal. But not a swinging back over the floor problem. But the rug comment is a good one, even for stained concrete floors, there's often a nice large fluffy rug for indoor/outdoor traffic...would at least offset that a bit. But I think they ought to be able to recess it at least a bit in the concrete, don't you?
(haven't discussed with the guys yet, trying to educate myself a little bit first...so I don't sound tooooooo ....whatever)
Sheila
OK so for the sliders: I live in mosquito-ville so we always have screen doors to open/close which interrupts the flow of traffic enough to let tripping not be an issue. Likewise people are 100% used to stepping down to the outside surface (deck, patio or stairs) which is not what I have, but still, it's natural for us to step OVER something... I do dislike how tall the interior thresholds are from an aesthetic standpoint, yes. My sliders are NOT recessed into the slab. That would have created several other issues WRT snow and water and drainage and forced the patio height quite a bit lower than my interior slab which I did not want.
Anyway, I guess one could just use foam insulation board or plywood to make a little step knockout, basically exactly the same as the formwork for a concrete step, only much shallower. This would require A LOT of pre-planning to get it exactly right front to back in the opening and you'd pretty much need to have the doors on site to do so. OTOH, the chances of getting it right and nice looking by cutting and removing the concrete post-pour seem a lot higher. I dunno other than it will take you micromanaging the crap out of the situation or you'll need a flatwork crew that is both meticulous and super smart which pretty much does not exist, IME, and especially not on a huge pour.
Post a Comment
<< Home