Big Progress on the Wood Fired Oven
It's FINALLY raining here, for the first time in what seems like at least a month, so I figured I'd take a minute to get you caught up with the wood fired oven project progress.
At my last check-in, we had dug and poured rebar reinforced footings and completed the formwork for the foundation slab. This bottom, structure-supporting slab is thick and reinforced with rebar and mesh, and it's an important yet fairly boring, non-rewarding part of the project.
Since I had calculated this slab was going to require close to a yard of concrete, it presented something of a dilemma. Based on way too much prior experience mixing bagged concrete by hand, I was SO not feeling the idea by-hand mixing the 35+ bags it was going to require, but when I called around to the ready-mix plant to get the price of having what's called a "short load" delivered, and then to the couple of on-site, small batch concrete delivery services I could find, the price proved to be just a little too outrageous to convince me we couldn't do it ourselves.
So, conceeding that we were in for another couple of adventures with bagged concrete mix, my next step was to call the local big box store and arrange to have this and all the other heavy stuff, ~65 80# bags of Quickcrete, 40 or so concrete blocks, and a bundle of 1/2" rebar, delivered to the house. All in all, it amounts to several tons worth of material that, to move by pickup truck and human power would have meant lots of driving and many exhausting trips. For $69, (any size) delivery seemed like a small price to pay, and it meant the driver could pull the pallets off the truck with his forklift and drive them right to my project site in the backyard. It was money VERY well spent.
On our next free Saturday, I towed home the largest gas powered concrete mixer our local equipment rental place had, and Boy and I got to work mixing and pouring:
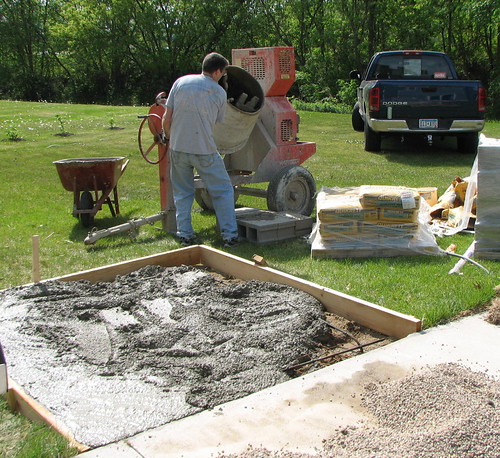
This slab ended up taking forty bags of mix. Not the kind of thing you can dilly-dally at, since the clock starts ticking on concrete curing from the minute you mix the first bag and it's critical to get all of the material in place while it's still fluid enough to be screeded and trowled. The mixer I rented could handle three bags at a time and while it was a slightly frantic couple of hours, the two of us managed to get the job done. Huge props to Boy for hoisting all those #80 bags up into the mixer. And props to me for being the only girl I know of that can wheel a full load of wet concrete. Fortunately the farthest I had to go with it was around the corner of the patio.
Here's all of the material in place, screeded and waiting to stiffen up a bit:
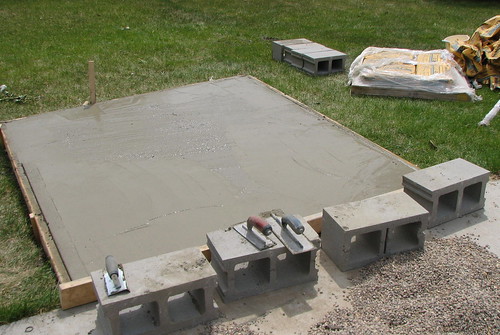
A couple of hours worth of curing later, all trowled up nice and smooth:

The next step was stacking the concrete blocks (CMU's) to form the base for the countertop height slab that actually supports the oven. These got "dry stacked" meaning they're set without mortar in the joints, and not having the mortar there to act as a buffer meant getting everything perfectly level was fairly tricky. Even the ~1/16" variation in level of the foundation slab made a difference, and we ended up putting a bit of sand mortar mix under the block in a few spots, (basically concrete mix without any gravel) to get the first course nice and level.
After that, it was back to work mixing concrete, this time two bags at a time by hand in the wheelbarrow, to fill every other core of the CMU's with a stick of rebar embedded in each. The remaining cores we stuffed with empty Quickcrete bags and leftover gravel to prevent concrete from falling into them when we poured the upper slab:

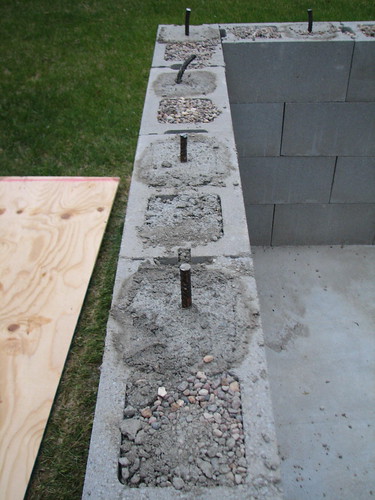
The angle iron you can see in the top photo is to bridge the opening in the base that will eventually be covered by a door of some sort. Rather than buy these couple of pieces of steel, I repurposed part of an old metal bedframe. Yay for recycling!
So there you have it. The boring parts are almost done, I promise. Next up...building the form and supports and pouring the upper "bridge" slab.
At my last check-in, we had dug and poured rebar reinforced footings and completed the formwork for the foundation slab. This bottom, structure-supporting slab is thick and reinforced with rebar and mesh, and it's an important yet fairly boring, non-rewarding part of the project.
Since I had calculated this slab was going to require close to a yard of concrete, it presented something of a dilemma. Based on way too much prior experience mixing bagged concrete by hand, I was SO not feeling the idea by-hand mixing the 35+ bags it was going to require, but when I called around to the ready-mix plant to get the price of having what's called a "short load" delivered, and then to the couple of on-site, small batch concrete delivery services I could find, the price proved to be just a little too outrageous to convince me we couldn't do it ourselves.
So, conceeding that we were in for another couple of adventures with bagged concrete mix, my next step was to call the local big box store and arrange to have this and all the other heavy stuff, ~65 80# bags of Quickcrete, 40 or so concrete blocks, and a bundle of 1/2" rebar, delivered to the house. All in all, it amounts to several tons worth of material that, to move by pickup truck and human power would have meant lots of driving and many exhausting trips. For $69, (any size) delivery seemed like a small price to pay, and it meant the driver could pull the pallets off the truck with his forklift and drive them right to my project site in the backyard. It was money VERY well spent.
On our next free Saturday, I towed home the largest gas powered concrete mixer our local equipment rental place had, and Boy and I got to work mixing and pouring:
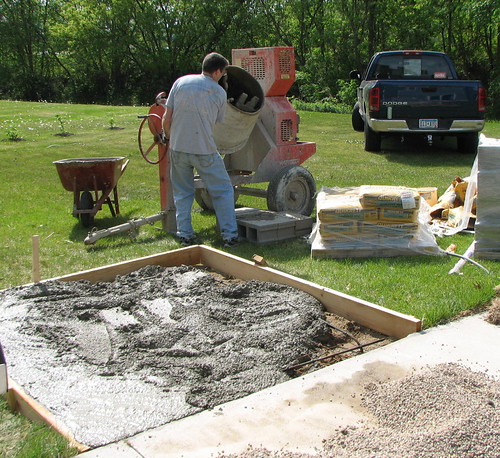
This slab ended up taking forty bags of mix. Not the kind of thing you can dilly-dally at, since the clock starts ticking on concrete curing from the minute you mix the first bag and it's critical to get all of the material in place while it's still fluid enough to be screeded and trowled. The mixer I rented could handle three bags at a time and while it was a slightly frantic couple of hours, the two of us managed to get the job done. Huge props to Boy for hoisting all those #80 bags up into the mixer. And props to me for being the only girl I know of that can wheel a full load of wet concrete. Fortunately the farthest I had to go with it was around the corner of the patio.
Here's all of the material in place, screeded and waiting to stiffen up a bit:
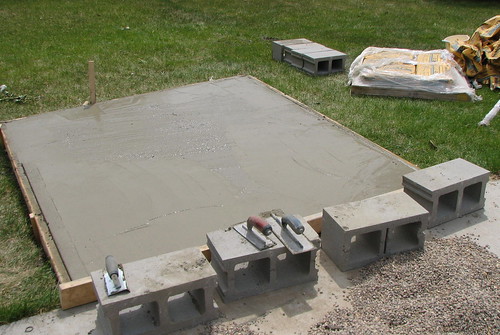
A couple of hours worth of curing later, all trowled up nice and smooth:

The next step was stacking the concrete blocks (CMU's) to form the base for the countertop height slab that actually supports the oven. These got "dry stacked" meaning they're set without mortar in the joints, and not having the mortar there to act as a buffer meant getting everything perfectly level was fairly tricky. Even the ~1/16" variation in level of the foundation slab made a difference, and we ended up putting a bit of sand mortar mix under the block in a few spots, (basically concrete mix without any gravel) to get the first course nice and level.
After that, it was back to work mixing concrete, this time two bags at a time by hand in the wheelbarrow, to fill every other core of the CMU's with a stick of rebar embedded in each. The remaining cores we stuffed with empty Quickcrete bags and leftover gravel to prevent concrete from falling into them when we poured the upper slab:

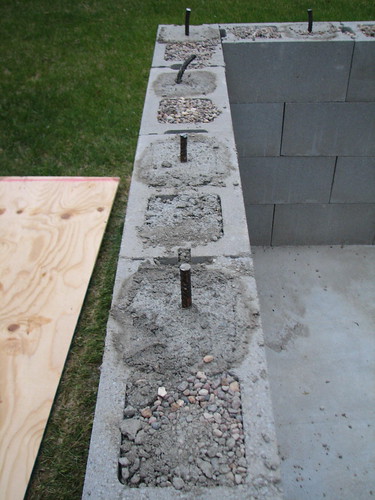
The angle iron you can see in the top photo is to bridge the opening in the base that will eventually be covered by a door of some sort. Rather than buy these couple of pieces of steel, I repurposed part of an old metal bedframe. Yay for recycling!
So there you have it. The boring parts are almost done, I promise. Next up...building the form and supports and pouring the upper "bridge" slab.
Labels: wood fired oven building
5 Comments:
did you guys scratch your names in the slab?
more, more! ... c'mon - I'm sitting here in Sydney, checking into your blogs sporadically and can't wait to see the pizza oven get finished. Ah well, I guess good things take time.
Good luck with it all!
Hi Splatgirl!
I hope that oven is going to be rendered/painted a nice bright colour :)
Any progress on the splatgirl mural in your studio?
Cheers from Oz.
how did you determine the size and spacing of the reinforcement?
Thanks,
Sara
hi sara
When it matters, a rebar schedule is spec'd by structural engineers based on load and span and whatever other forces will be at play. Meaning technically, there IS a right way, but that's completely unimportant for a project like this since it's not REALLY holding much up and no lives depend on it.
My 4" thick floor, patio and driveway slabs all have rebar in a 2' grid.
This slab was 6" and IIRC I set a perimeter of rebar that's tied to the footing reinforcement and then a sheet of mesh tied to that.
As they say, no one has ever said "darn, I wish I had put LESS rebar in that slab".
Post a Comment
<< Home