December 3rd, Footings
By the end of November we were ready to roll. Our permits had miraculously been issued after a few minor hangups and I raced to coordinate our team to get the ball rolling for real. What a thrill!
(Originally posted to LiveModern 1/28/2005)
In a previous post I talked a little about excavation and there's more to that story that I think is worth telling so I'll start there.
During excavation, first the the lower floor level grade is established and then the footing trenches are dug down from that to below the frost line. In our case, the backhoe took two scoops to get down to footing depth, saw the soil conditions and immediately stopped digging. Here's where I stopped breathing.
One of the things I had been emphatically advised to do by my GC uncle was to get soil borings done while the land was in escrow, to be certain we were purchasing land that was buildable. Borings and a soil report were bid in the neighborhood of $2-3k based on my phone calls to geotechnical/soil engineers which would be unrecoverable funds should the land sale fall through. Since the surrounding land is developed and this lot had never been bought or sold previously, I reasoned that the chances of the soil being unbuildable were slim, and decided against getting borings done prior to closing. THIS WAS A HUGE RISK, and I don't think I'd take it again. Discovering non-bearing soil conditions would have meant either falling out of escrow, tens of thousands of dollars worth of correction (i.e. digging out non-bearing soil, hauling away and replacing), or being stuck with land that you can't do anything with. (I've been told that non-buildable lots are actually bought and sold all the time by people who don't bother to investigate the soil conditions prior to purchase [ha!imagine that], discover poor soil after the fact and then re-sell the land to the next unwitting buyer.) For sane people, it would presumably be ideal to know you can't build on your $100k worth of land BEFORE you've got several thousands of dollars invested in design, plans, permits, digging, etc, and your whole team sitting on site at the ready. Maybe I'm a little more sane now...
As our story ends, my excavator happens to keep a soil engineer on call. After the two fateful shovelfuls by the backhoe, I held my breath and tried not to have a nervous breakdown while we all waited ($$ flying away as equipment and labor sits around) for the engineer to arrive and take soil samples. Two hours later, he announced that there was good bearing soil slightly deeper than our desired footing depth around the entire building pad, which meant we could proceed and just needed to dig a deeper footing. WHEW. So for the extremely agreeable price of $600 for a site visit and soil report by the engineer, and the few hundred dollars worth of materials for a taller frost wall, we dodged what would have been a very expensive, miserable bullet. Note to self: could have avoided this all by getting soil borings in the first place like uncle said. On the other hand, it turned out OK and we're building our house on a beautiful lot that we might have otherwise been afraid of buying if we had had soil borings done in advance.
Here's a few pictures of our footings getting set up and poured. For those of you from warmer climates, those big black and white floppy things in the trenches and piled around are frost blankets that are used to insulate the ground until the foundation is in and backfilled. One of the many complications of winter construction in MN.
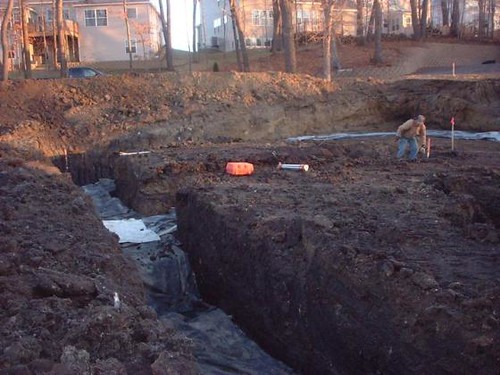
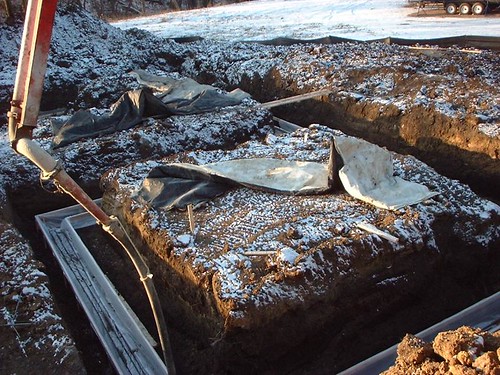
Access issues meant the first of what has so far been a few visits by the pump truck which is the big boom/hose thing you see (the expense of a pump truck is one of the necessities of ICF construction as well). Basically a giant arm that supports a hose unfolds and extends from a huge truck designed specifically for pumping concrete wherever it needs to go. Concrete flow and the movement of the boom is operated by remote control just like a real life video game while a guy in the trench or on the wall holds the outlet end. Pretty neato and also very expensive. I've said several times that the greatest shopping trip I could imagine still wouldn't equal the speed with which money is spent when the pump truck is on site. You can practically watch dollars come out of the end of that hose.
Our ICF guy, Jeff Schultz of Concrete Building Supply formed and poured our footings using a cool product called FastFoot It's basically just a big three sided plastic bag that comes on a roll that's stapled over a ledger board to form the footing, replacing the much more labor intensive means of building footing forms out of wood. Once the stakes and ledger are in place, it's just simply unrolled into the footing cavity and you're ready for rebar and concrete, plus it's waterproof so it prevents the footing from wicking ground water up from underneath. It's one of the many products that's a huge improvement on mainstream methods but has yet to become mainstream.
(Originally posted to LiveModern 1/28/2005)
In a previous post I talked a little about excavation and there's more to that story that I think is worth telling so I'll start there.
During excavation, first the the lower floor level grade is established and then the footing trenches are dug down from that to below the frost line. In our case, the backhoe took two scoops to get down to footing depth, saw the soil conditions and immediately stopped digging. Here's where I stopped breathing.
One of the things I had been emphatically advised to do by my GC uncle was to get soil borings done while the land was in escrow, to be certain we were purchasing land that was buildable. Borings and a soil report were bid in the neighborhood of $2-3k based on my phone calls to geotechnical/soil engineers which would be unrecoverable funds should the land sale fall through. Since the surrounding land is developed and this lot had never been bought or sold previously, I reasoned that the chances of the soil being unbuildable were slim, and decided against getting borings done prior to closing. THIS WAS A HUGE RISK, and I don't think I'd take it again. Discovering non-bearing soil conditions would have meant either falling out of escrow, tens of thousands of dollars worth of correction (i.e. digging out non-bearing soil, hauling away and replacing), or being stuck with land that you can't do anything with. (I've been told that non-buildable lots are actually bought and sold all the time by people who don't bother to investigate the soil conditions prior to purchase [ha!imagine that], discover poor soil after the fact and then re-sell the land to the next unwitting buyer.) For sane people, it would presumably be ideal to know you can't build on your $100k worth of land BEFORE you've got several thousands of dollars invested in design, plans, permits, digging, etc, and your whole team sitting on site at the ready. Maybe I'm a little more sane now...
As our story ends, my excavator happens to keep a soil engineer on call. After the two fateful shovelfuls by the backhoe, I held my breath and tried not to have a nervous breakdown while we all waited ($$ flying away as equipment and labor sits around) for the engineer to arrive and take soil samples. Two hours later, he announced that there was good bearing soil slightly deeper than our desired footing depth around the entire building pad, which meant we could proceed and just needed to dig a deeper footing. WHEW. So for the extremely agreeable price of $600 for a site visit and soil report by the engineer, and the few hundred dollars worth of materials for a taller frost wall, we dodged what would have been a very expensive, miserable bullet. Note to self: could have avoided this all by getting soil borings in the first place like uncle said. On the other hand, it turned out OK and we're building our house on a beautiful lot that we might have otherwise been afraid of buying if we had had soil borings done in advance.
Here's a few pictures of our footings getting set up and poured. For those of you from warmer climates, those big black and white floppy things in the trenches and piled around are frost blankets that are used to insulate the ground until the foundation is in and backfilled. One of the many complications of winter construction in MN.
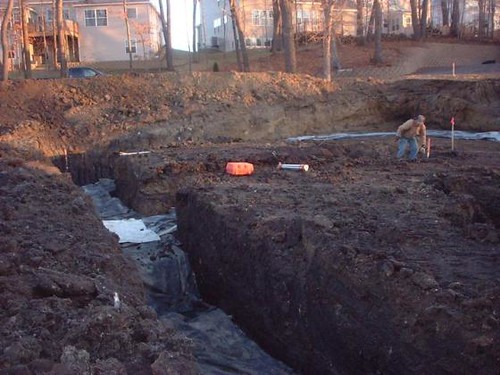
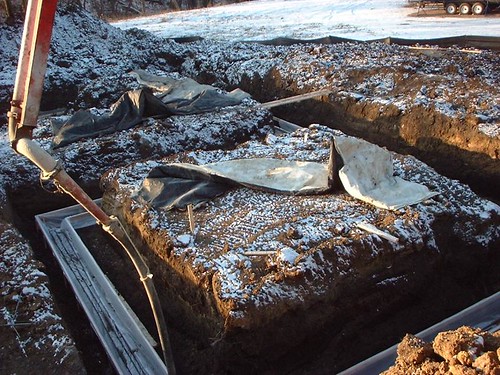
Access issues meant the first of what has so far been a few visits by the pump truck which is the big boom/hose thing you see (the expense of a pump truck is one of the necessities of ICF construction as well). Basically a giant arm that supports a hose unfolds and extends from a huge truck designed specifically for pumping concrete wherever it needs to go. Concrete flow and the movement of the boom is operated by remote control just like a real life video game while a guy in the trench or on the wall holds the outlet end. Pretty neato and also very expensive. I've said several times that the greatest shopping trip I could imagine still wouldn't equal the speed with which money is spent when the pump truck is on site. You can practically watch dollars come out of the end of that hose.
Our ICF guy, Jeff Schultz of Concrete Building Supply formed and poured our footings using a cool product called FastFoot It's basically just a big three sided plastic bag that comes on a roll that's stapled over a ledger board to form the footing, replacing the much more labor intensive means of building footing forms out of wood. Once the stakes and ledger are in place, it's just simply unrolled into the footing cavity and you're ready for rebar and concrete, plus it's waterproof so it prevents the footing from wicking ground water up from underneath. It's one of the many products that's a huge improvement on mainstream methods but has yet to become mainstream.